Maybe the most challenging aspect of our working lives is bringing new things to life and have people using them. This is particularly true for industrial designers, whose job is to combine functionality with aesthetics, and create things others love.
We’ve had the pleasure of meeting Claas Kuhnen and learn about his recent challenge: addressing functional design in today’s digital times. Besides running his own studio, Claas is also teaching at Wayne State University focusing on 3D design and fabrication technologies. His work was also present at exhibitions like SOFA, SNAG and SIGGRAPH.
Very excited to learn more about product design from an insider, and see some of Claas’ brainy creations.
Marius Iatan: Can you share with us what is your creative process when designing a new product? Where do you look for inspiration?
Claas Kuhnen: Industrial design is a very research driven discipline. Sometimes the right initial idea can be sufficient, but often you need to fully understand the broader picture. And research itself can really help as an inspiration simply because the deeper you try to understand a subject matter, by reading about it, sketching ideas, browsing photos, testing and experiencing a product, interviewing others and such, you sooner or later will find the building blocks you can later craft together into a cohesive design proposal. It is often like playing a puzzle. With time and work, results will emerge.
However products don’t always have to be solving a new problem. They can also be simply beautiful to look at. It’s the same with art, which can be critical and thought provoking, or just pleasing to the eye and for your enjoyment.
Marius: You have a very complex background, from graphic to product design, with a focus on the latter. Can you tell us what you have been working on recently?
Claas: In the past year I was working on many furniture projects for clients such as Leland International but also Integra who makes the airport business lounge furniture for American Airlines. The owner at 2B Studio is fortunately very open to whatever process and CAD software I use as long as in the end I can deliver data the engineers can utilize for manufacturing. I very much enjoyed those projects because I was able to research the usability of a subdivision surface modeling process to furniture design which consists of hard edge elements such as wood parts, and soft elements such as upholstery. Blender proved to be radically faster and more productive for the concept ideation and rapid prototyping phase than my parametric solid modelers. Traditionally, those CAD applications are weak when it comes to speed and organic shapes.
In the end, my client 2B Studio was very pleased with the results. The workflow allowed us to quickly and cost effectively generate and explore ideas and the CAD data was sufficient for the client’s in-house manufacturing department.
Marius: Your work has been showcased at fairs around the world. Has this helped your career, or is it just a self rewarding experience?
Claas: I think it is both. It is of course great when you see the products you worked on being showcased at the industry’s most important commercial furniture event here in the USA. However, this is more like the whipped cream on a cake. The most important take away is what you can learn from such projects and how you grow as a designer refining your workflow, technical abilities, and in general your design sense. This carries more weight in your portfolio.
Marius: When did you start using Blender? Is there an interesting story hiding there?
Claas: I think it was 2002 when a fellow student in my color design major told me to look into Blender because a friend in South Africa told him about it. That was during a time when there was no native OS X build, but I liked the UI and the idea of having 3D modeling, animation, and post-processing inside one application. When I entered the graduating school for jewellery design I used Maya a lot because it is polygon and NURBS based, but I needed the ability to work on any computer I had access to, and at that point in 2005 Blender was available for Mac and Win equality. So I often had a jump drive with my work and Blender builds.
My 3D animation and digital arts professor was not very convinced about Blender at that time because of the UI and, well, Maya is just an industry standard. I introduced few of the animation students to Blender and some of them used it for better UV unwrapping or speed modeling. That was the time when even Maya users recommended online to use Blender for that particular task. Two students even switched completely to Blender while working on their game design projects with the new Unity game engine back then.
Marius: Is your entire pipeline based on Blender at this moment?
Claas: I use Blender not only for rendering but also for tasks such as concept ideation modeling, prototyping and actual product design. In my workflow I currently pair it with Autodesk’s Fusion 360 which is a new parametric solid modeler. Fusion 360 offers a technology (T-Splines) that allows you to sculpt with polygons and the software resurfaces the sub-d model with perfectly fitting NURBS patches. That is quite fantastic. In the past as a product designer you were not able to meaningfully use polygons for product design and certain organic shapes were very difficult to surface just with a NURBS approach. The fact that Blender is object oriented and offers modifiers, allows me to work in Blender like in Autodesk Fusion/Alias, meaning I use Blender in a way that mimics the process I have to use in CAD (for example Blender’s boolean modifier command I use to cut, trim, or join objects). It is a common process in Alias to work on hard edge models for the concept phase and only for the finale prototype to round product edges. The shrinkwrap modifier is equal to the project and surface flow command. It allows me to wrap a surface over a target. This, for example, can be used to quickly resurface/rebuild an upholstery model with a cleaner mesh, or project a geometry pattern onto a surface and then combine that with the duplicate function so I can instance—lets say— small spheres over a handle surface.
NURBS obviously is more precise, but slower, and polygons, in this case, are dramatically faster. The mesh data allows me to even save different variations into the same file—so for one object I can have few ideas and swap them out by just selecting a different mesh data block. And thanks to T-Splines all the work I do in Blender I can then transfer into Fusion, convert to NURBS. This is like a dream come true.
Let me illustrate this with a project I worked on in 2014 where I was tasked to design a furniture solution for the Beachstone series for Leland International, for the upcoming NecCon 2014 furniture exhibition.
Beachstone is a furniture set that is inspired by the nature and rounded stones so the product should not have very linear forms, but rather very smooth and organic characters, something that is very hard to do with NURBS but very easy with subdivision surface modeling.
1. Early backrest ideation studies
It all started with some very basic 2D profile drawings I got which I needed to translate into 3D shapes and then explore different form and volume ideas with the side goal to possibly create a modular configuration system.
2. Design and Rapid Prototyping phase
The next step was to create a 3D model that only included the fabric skin. This model was used to mill a life size foam model to verify comfort and fit. Once the shape was finalized upholstery foam material in Blender was projected inwards so I was able to understand where a supporting wood structure would be needed. The wood construction was send to Fusion 360 where I converted the polygon mesh into NURBS models to test for stress issues and generate the 3D step model for the engineer and tool path for the CNC router to mill the wood parts and foam core backrest for manufacturing.
3. Promotional Material
Showing the actual exhibition booth and digital renderings done in Cycles and calculated on RenderStreet.
Marius: What kind of project gives you the biggest satisfaction when it’s finished? And what kind of project inspires you the most?
Claas: In general I love projects where I can learn about something new. You will be surprised how much you start to learn about yourself and our environment this way. You start seeing facts and connections you were not aware of before, even while they were right in front of you the whole time. Generally, I find the projects most interesting when they have a certain social or cultural importance or value. Obviously in a commercial world you have to sell your product. But if, in addition, the product can change the consumer’s behavior to the better, or teach them a little, it is very rewarding.
Marius: How often do you use 3D printing in your work? How do you think this technology is going to change the way 3D artists work?
Claas: 3D printing is a pretty fantastic field. The problem with hand sketches or 3D CAD models is that you cannot touch them, you cannot experience them, and thus learn less from them. You actually do make sketches and CAD models to find answers to certain questions and 3D printing now makes the generation of actual 3D models so much easier and cost effective. Hand model making skills are great to have but you cannot beat a 3D printer when it comes to precision. So specifically for ergonomic questions this is fantastic. What will really be interesting is to see is where in the end this technology will find it’s true purpose in the maker scene. The problem is that the average person will not really be able to use 3D printing well because most of the time they lack the ability to create the 3D data they need. And the current hot topic is print on demand for mass-production with a certain required quality. Currently most 3D printers still have some good quality 3D print material compared to injection molded parts. Last year at the Autodesk University in Las Vegas, I saw a a company from London that makes custom dolls and they are all printed and painted on demand. That’s a really fantastic idea and process that allows designers like myself to produce products without the need of a factory. I think this is where the future in 3D printing lies. That’s also something we highly focus on here at Wayne State educating out students to be future small scale entrepreneurs.
Marius: Eliel Saarinen said “Always design a thing by considering it in its next larger context—a chair in a room, a room in a house, a house in an environment, an environment in a city plan.” Is this something you take into account when you design your products?
Claas: To be a good product designer you have to take into consideration nearly everything. You have to see things in the bigger picture – how everything influences the other, connected like a spider web. Otherwise, you might miss out on future additional design leads, or even create a product that might not work well in a certain situation. Oddly this philosophy is often ignored. Many companies employ an ethnographic research and manufacturing process that develops a solution to an isolated need. So the new buzz word now is design anthropology which tries to put a focus on the surrounding of a product, including the culture. At the end, there always has to be meaning to your product which can have many forms.
Marius: You are also teaching industrial design at Wayne State. How does teaching complete your other professional activities?
Claas: Teaching and working is a pretty great combination. In a company you will be restricted to the workflow and tools that are accepted and thus it is likely that you might miss out on the latest changes and alternatives, specifically when the topic of industrial standards is concerned. With teaching, you have the ability to freely explore a new direction and sometimes this leads to quite interesting observations. Nearly my complete workflow is influenced by the research. I personally do not care about industrial standards, because the industry in general is too slow to adapt. While your work should be able to be transferred, I think the competitive advantage is not being compliant alone, but in being compliant while being progressive.
Smaller employers are more receptive to that way of teaching because I think larger companies are just less flexible to evolve because they are well too big.
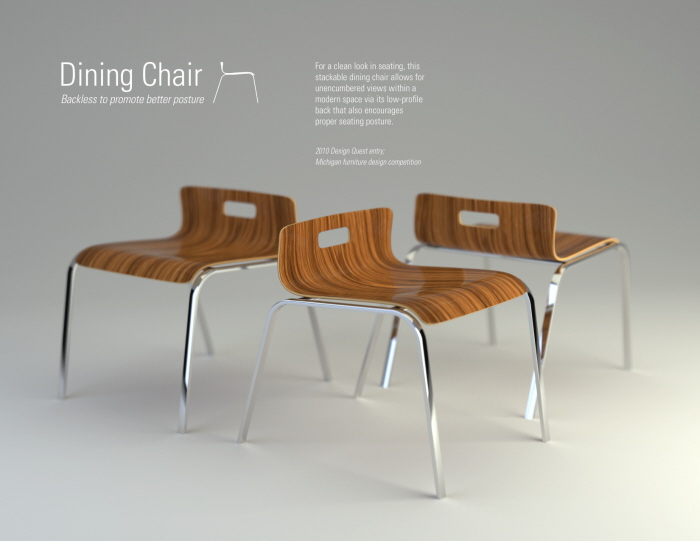
Our own favorite chair designed by Claas Kuhnen
Marius: They say that you are not a real designer until you create a new chair. Can you think of a chair design that you admire? And from your own work, which chair is the star of your portfolio
Claas: You ask me one of the hardest question because I personally never really know what I like. I grew up as a designer in Germany and thus was exposed to European simplicity and clarity, but at one point this got too boring for me. When I started to study and work in the US I found the decorative elements there very interesting. While, in my opinion the US has too much an affinity with traditional designs and office furniture is often very boring and conservative, for me the ideal mix in design became a mix of both. Simplicity for the sake of clarity, but a little decoration here and there as a gentle detail. The furniture I love the most is that with hidden surprises. For me however furniture also has to fit into the environment. So I am not sure if I a real designer yet because I am still in flux and changing my taste. But if you would ask me right now, I would like chairs that use clean surfaces where geometric shapes are cut or added to it. I dont know why, but I really like that classic modern juxtaposition. Must be my age ; )