What do you do when you dream of something but you don’t have the ready-made tools for building it? You take things in your own hands and build your own tools.
We continue our guest post series with an exciting story, coming from Radu, the man who built up a 3D scanner from scratch.
If you haven’t heard about my city, you certainly heard about Trrransylvania! Well, that’s were Cluj is. Nope, I haven’t met any vampires (yet!) but I surely met lots of IT guys around here. With more than 10.000 people working in tech companies, Cluj is also arguably called the Sillicon Valley of Eastern Europe… Funny enough, the startup that I am working on right now was born in the real Silicon Valley. More exactly, in Palo Alto.
Tulemod is the typical tech startup, built by technology enthusiasts, trying to change the world by developing a disruptive technology. Our vertical is the fashion industry and we’re working on a solution for digitizing apparel and enabling users to mix and match looks online with the maximum realism. It might seem an utopia but it’s actually a challenging problem that can be solved using a mixture of computer vision, 3D modelling, 3D graphics and enough programming.
In April 2014, after an amazing week in the Silicon Valley, where I met the founders and the investors that support this project, I came back to Cluj decided to make Tulemod a success. The first challenge was to solve the “3D scanning” of the garments. And the first idea was to use a 3D sensor, such as the Kinect. With a long cable, one could scan a dressed mannequin. The task was quite tedious as the user had to swipe the mannequin with the scanner repeatedly, turning around it. And taking care not to trip on the long cable! We thought that the user should rather stand still and make the mannequin turn. Thus, we improvised a turning table using an old chair of mine which was swung by a… piece of rope! Now the scanner needed two people: one for pulling the rope and another one to scan the mannequin. But hey, for an MVP we found a cheap solution – provided that the salary of the guy pulling the rope was lower than buying a motor : )
But there was still a problem with the dresses. The slightest rotation would make most of the dresses change their shape and eventually ruin the 3D model. Also, the Kinect is not accurate enough and we couldn’t get all the necessary details for a realistic 3D model. Then, I turned my attention to coded structured light, an old acquaintance of mine. But we would have problems with the coloured garments… and the market of black and white garments was too narrow. However, combining photogrammetry with black and white structured light proved to be a reliable solution. So, we started working on a scanner that could shoot simultaneously the subject from different angles while also projecting a pattern for obtaining the correct structure.
This time, always faithful to the MVP philosophy I used … broomsticks to hang the cameras. I had a hard time explaining the sales person that I work for a research project and not for a cleaning company. Of course, the brooms had to stand vertically so we bought supports for table legs. This time, another sales man will remember me as an undercover carpenter. Finally, the cameras are attached using custom supports that we built with our own 3D printer.
The scanner was built eventually using 60 cameras, 250 meters of ethernet cable, five network switches, 6 power sources, 40 broomsticks, 50m of led band and more than 280 screws.
Our new scanner is very flexible because the cameras can be placed as far or close as needed from the object to be scanned. So, we can scan objects from the size of a shoe to the size of an adult person. The accuracy of the 3D model is high enough for 3D printing the objects and the quality when superposing the texture onto the mesh is excellent. Another advantage of this scanner is the scanning speed. All the cameras are triggered simultaneously so we can even scan a talking face or a child. The resulting 3D scan is an OBJ file, a well known 3D format that can bet used by all major 3D editing software.
However, if you understand photogrammetry, you know that not everything is so bright. Some surfaces are not easily scannable so we have to develop solutions for the transparent surfaces, the hair and the reflective or the bright surfaces.
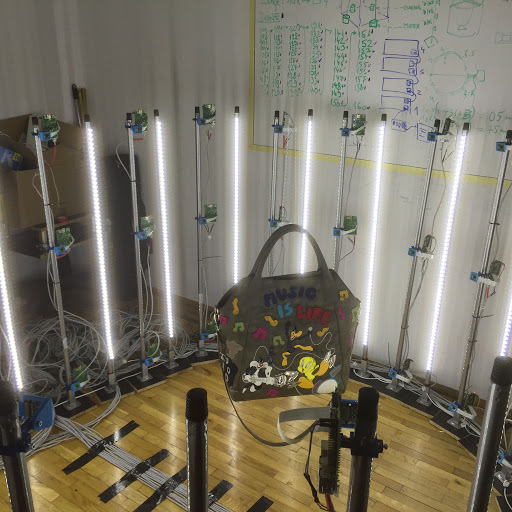
Scanning a handbag
The applications of 3D scanning are quite obvious in traditional fields, such as the medicine, industrial applications, media and design or heritage preservation. The current development of VR (Virtual Reality) and AR (Augmented Reality) open new horizons for using 3D objects. With a VR headset, the users can immerse themselves in movies from the perspective of the main character, dance on the scene next to a music star, view and understand products from advertising spots, work together with remote colleagues or participate to courses and inspect 3D models.
We have a long road ahead as there are still many improvements to be made. On our short list of future improvements are the machine learning techniques for refining our algorithms and moving some of the processing in the cloud with providers such as RenderStreet.
We are well aware that we are just at the beginning of a long journey but we are happy that we made the first steps. This is the time and the place to build our project. A few years ago, this scanner would have been just a dream. Nowadays, we have affordable cameras and processing units, fast processors and large amounts of memory readily available. So, we just have to use the hardware and the software tools, work hard and dream big!
Radu Orghidan was born in Romania and lived and worked in Spain, France and Japan. His expertise is in the computer vision field, mainly 3D reconstruction. He is currently with Tulemod, USA, developing an innovative solution for the 3D scanning of fashion items… and his own kids.